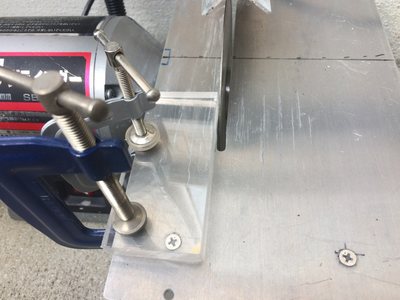 | 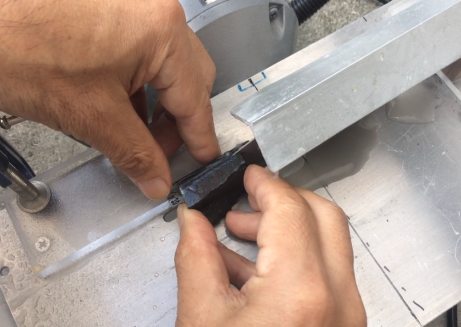
|
We made a sawing guide using a acrylic plate and small cramps. The space from the diamond blade is adjusted 1.5mm.
| Cutting the sample. Take care of your finger not touch to the blade, or you get a small burn. Click to see a movie!
|
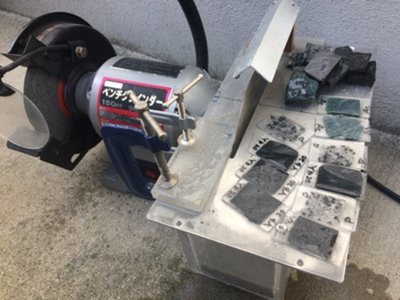 |
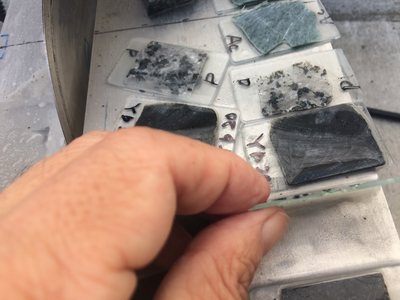 |
After cutting, the sections become around 0.5mm thickness on the glass. The front water cover is removed.
|
Close up of the section. 0.3 to 1.0 mm thickness is the best.
|
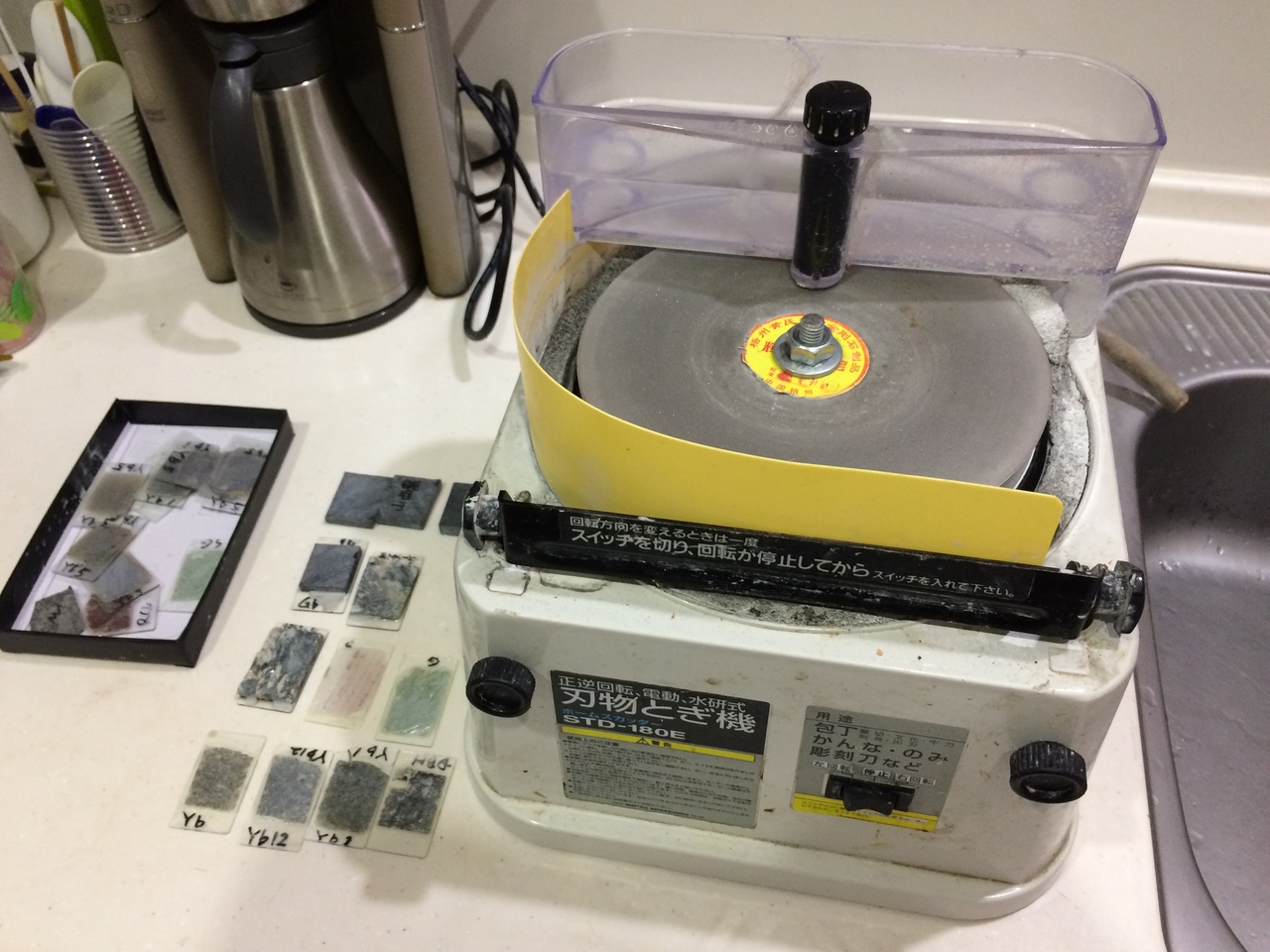 | 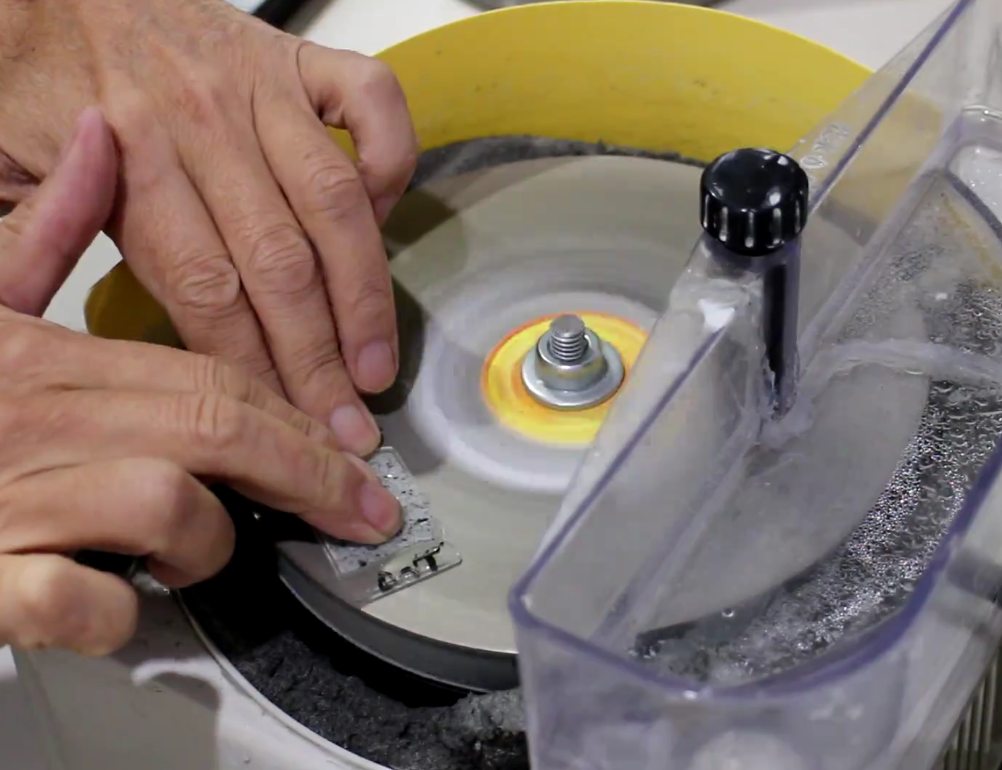 |
Secondary grinding begins with our home-made machine.
| Rock grinding! Click to see a movie! #180 grit diamond plate. You can reduce the thickness to 0.1mm or less.
|
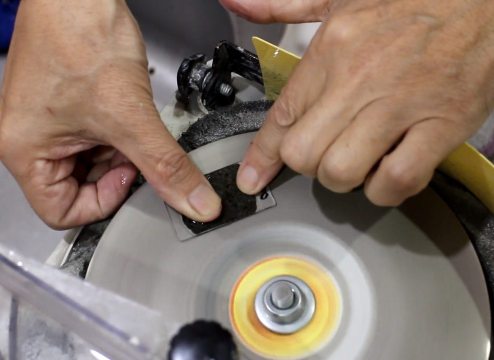
|
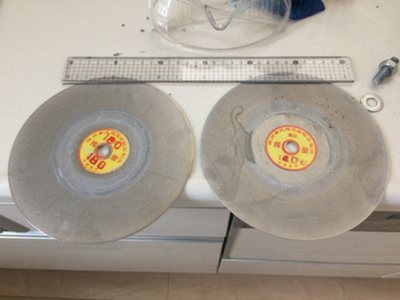 |
Another grinding for a basalt section. You can see the section is going to thinner. Click to see a movie!
|
If you need the next step, you can
use #400 to #600 grit disks again for the second stage. However, usually
no need. Now, I only use #180 normally.
|
|
|
Close up of grits. Left: #180 Right: #400 Width of the image is about 20mm.
| If you do not have the machine, You can use the diamond plates #150 or #400 as same as the rotating tool.
|
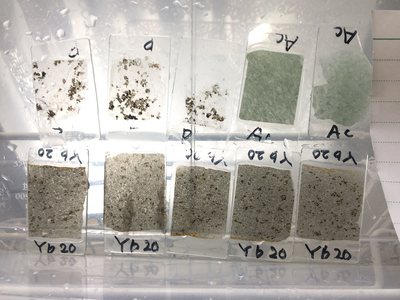 |
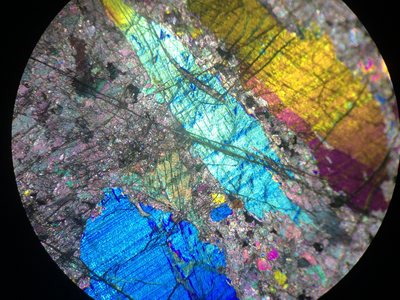 |
0.1mm thickness or less, you can go to the second and final grinding.
| If you only use the diamond plates, you can not erase the above slick lines. So we need the next hand grinding stage.
|
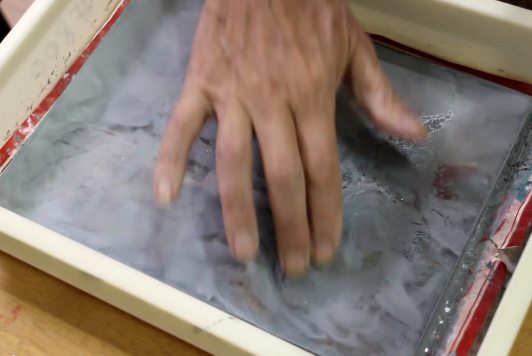 
|
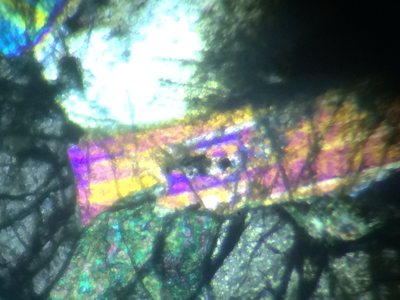 |
#800 carborundum grinding on the glass plate. Click to watch a movie!
|
Check the thickness using the
polarized microscope. Colorful interference colors of feldspar or quartz
show the section is too thick. So more grinding is need.
|
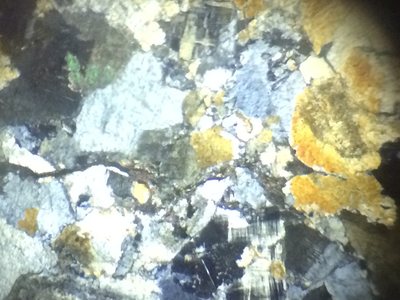 |
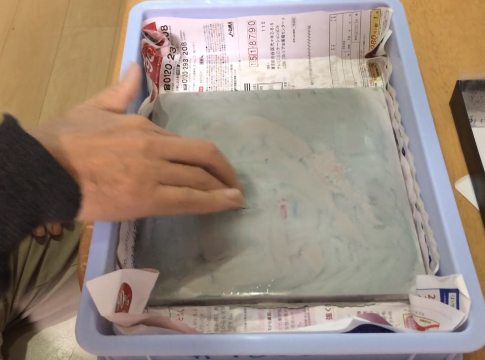
|
The interference color turn to
thin yellow to white cream, you can move to the final grinding #1500 or
#2000. The frequent thickness check with the polarized microscope is very important.
|
#1500 alundum grinding as the final
stage. Click to see the movie! The purpose of final stage is to make
smoother the former rough surface. If your section shows still strong
yellow color for feldspar or quartz with the cross polar view, it means
too thick, so you have to return the former stage #800.
|
|
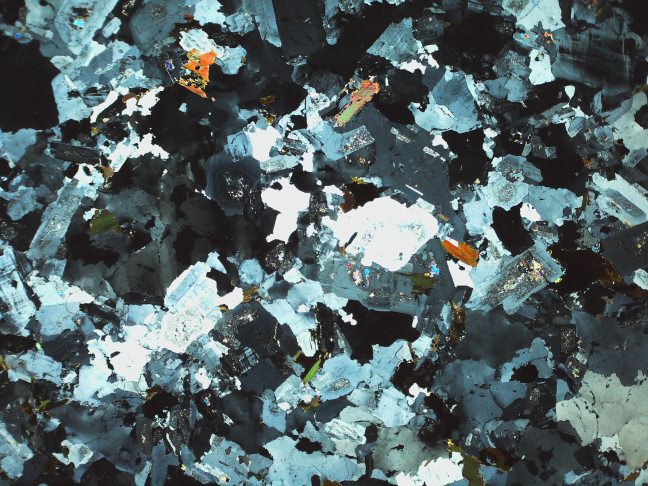
|
A completed thin-section, Both-mica Granite in Kanchenjunga, Nepal.
|
Cross polar 13.5mm width, Both-mica Granite in Kanchenjunga, Nepal.
|